CUSTOM
THERMOFORMING
Formex Manufacturing
Inc. offers a competitive turnkey service for custom thermoformed
plastic projects. Our services include design, tooling, forming,
CNC trimming and additional secondaries. Besides conventional single
sheet forming and twin sheet forming techniques, our specialty is
twin sheet products with encapsulation features.
Design
Ideas, concepts, and final 2-D or 3-D files are successfully
accomplished for your thermoformed plastic project by our team of
experts specializing in reducing part cost without sacrificing effectiveness.
Tooling
Cast or machined aluminum molds with temperature control and
optional blow and exhaust pins are designed to exact specifications
required for your part. We work with a number of pattern makers,
foundries, and machine shops to optimize quality and price.
Forming
Simultaneous
Twin Sheet Pressure Forming - Two sheets of materials are
heated with a three tier sandwich oven and formed at the exact same
time on two different mold halves that have mating pinch line geometry.
The opposing molds press together and internal vacuum sucks the
plastic to the heated molds. At the same time blow pins propel inside
the cavity and release 50 � 120 psi air pressure to ensure crisp
part detail. The two halves of plastic are fused together at the
pinch line with heat and pressure. The result is a single hollow
body plastic part. The simultaneous process is effective with thinner
gauge materials where the speed of material cooling too soon jeopardizes
a quality bond.
Sequential
Twin Sheet Pressure Forming � Same as above except the two
sheets are heated in separate two tier sandwich ovens and the molds
are formed in sequence one at a time. The sequential process is
effective with thicker gauge materials which require a more efficient
heating process.
Encapsulation
� Used with either simultaneous or sequential twin sheet forming,
a structure (wood, foam, metal, etc.) is inserted before the two
mold halves press together. The result is a double wall part with
localized internal reinforcement.
Single
Sheet Pressure Forming � One sheet of material is formed
on a mold with standard vacuum. In addition, a box is placed over
the cavity and 50 � 120 psi is applied to force the material into
all details of the mold.
Single
Sheet Forming - One sheet of material is formed on a mold
with standard vacuum. Plug assist, billow forming, or snap back
techniques are used to manipulate material distribution.
CNC Trimming
Formed plastic parts are located on a vacuum fixture. A 5-axis
7.5 hp router travels around the part trimming out all perimeter
run out and internal cut outs, holes, slots, and vents.
Additional
Secondaries - |
Solvent
bonding
Adhesive bonding
Fabrication
Polyethylene welding |
MULTI COMPONENT
PROJECTS
|
TWIN SHEET PAD WITH EPS FOAM
ENCAPSULATION
|
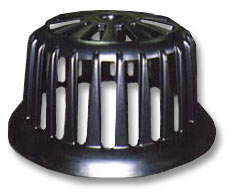
33" TALL SINGLE SHEET
|
HOLLOW TWIN
SHEET
|
|